Automatic feeding system for a production cell.
● Introduction
Project information
Automated feeding and quality control system for machining cells, which selects raw materials and prevents defective parts from entering the production process.
This project consists of designing a system capable of feeding a processing cell composed of four machines that carry out the machining process, while simultaneously selecting the raw material to prevent defective or incorrect pieces from entering the first machine—parts that would otherwise need to be discarded later for being damaged or not matching the desired specifications for machining.
To meet the project's requirements, we have implemented various systems.
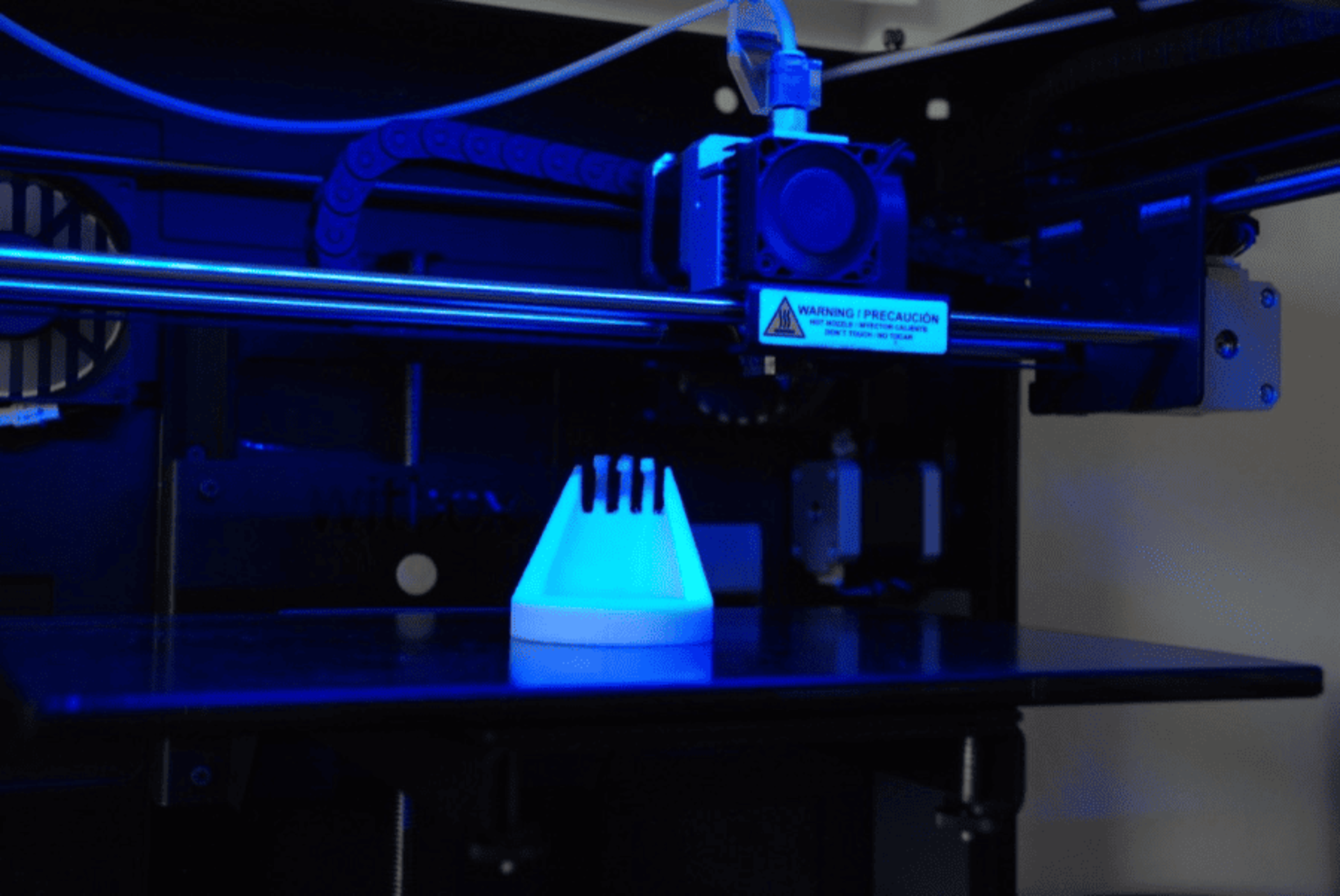
Machine Vision
This system consists of a camera and a PC, both specifically designed for machine vision.
Using this system, together with a conveyor belt and lighting specifically designed for the application, we perform raw material selection and transmit the coordinates to the robot for picking the part.
The PC managing this system communicates with the robot via Ethernet.
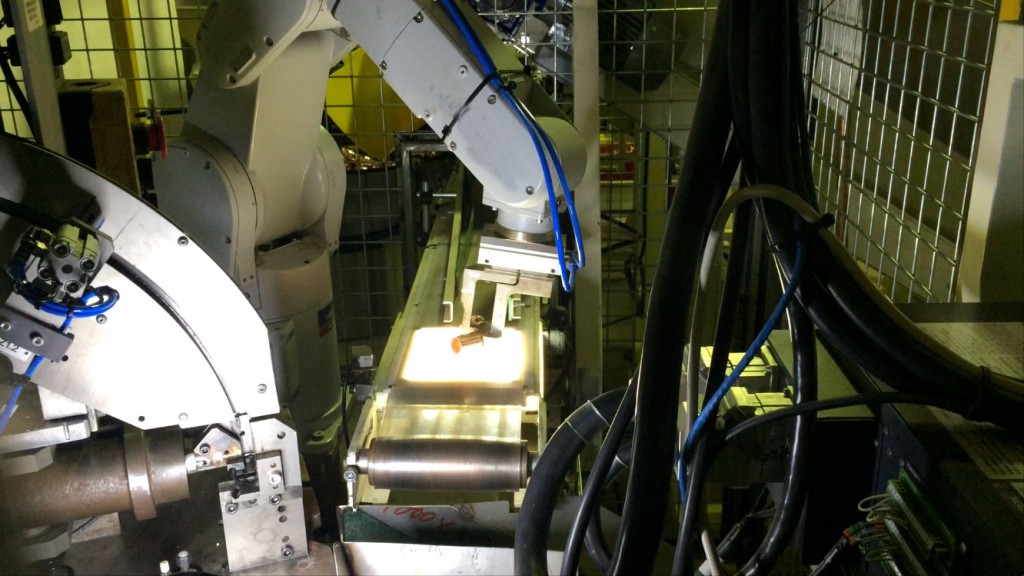
Robot
The robot selected for this project is a SCARA-type with 4 degrees of freedom and capable of handling a payload of up to 12 kilograms at its end effector.
It picks up the part identified by the vision system using vacuum suction and places it into the first processing machine.
The robot communicates with the vision system via Ethernet and with the PLC through digital communication.
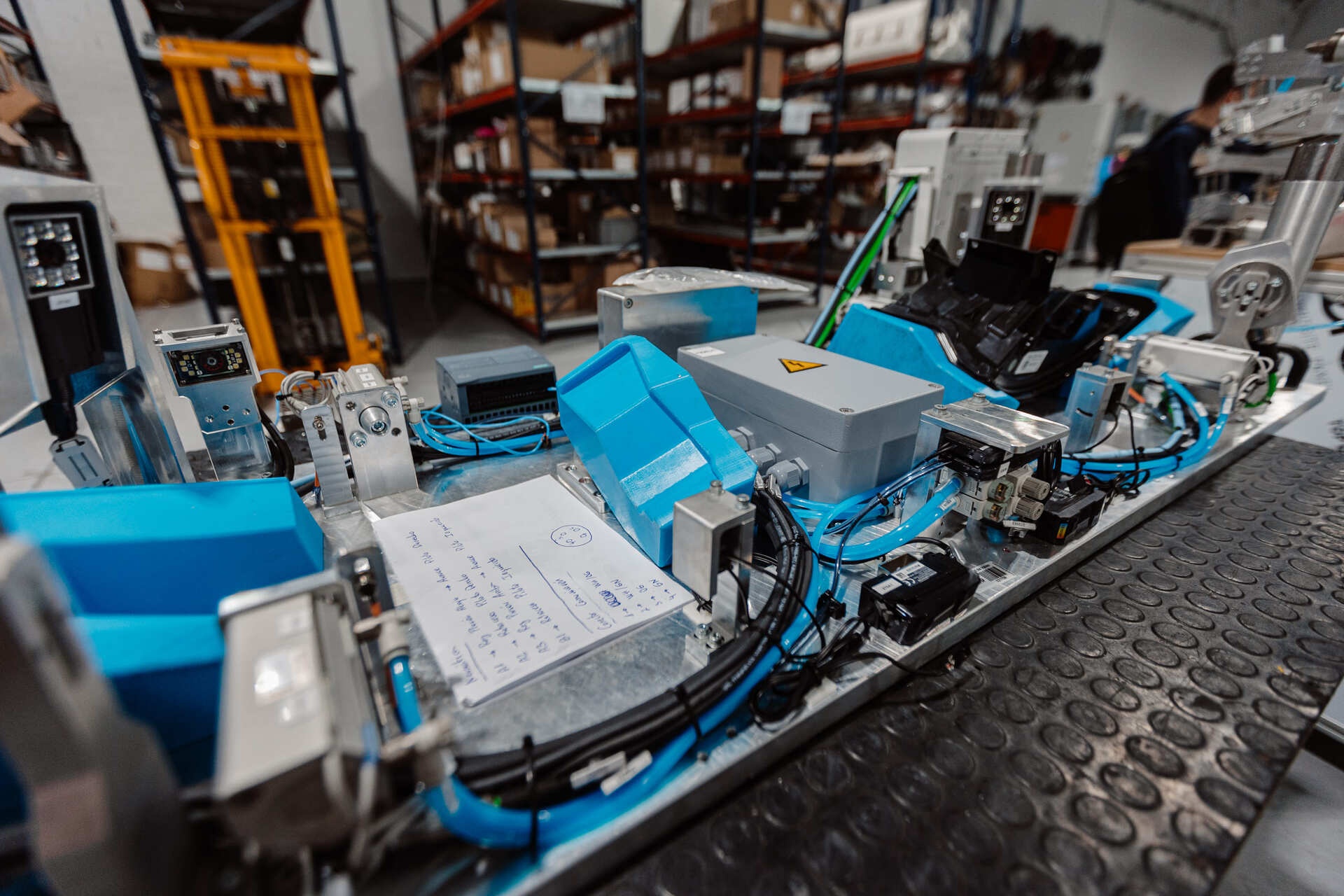
Transfer
The transfer system consists of a 6-meter-long aluminum linear guide, 3 processing heads, and a servomotor for precise positioning.
It picks up the finished part from each machine using vacuum suction and transfers it to the next one to continue the machining process.
The control of the 3 heads in the transfer system is managed by the PLC in digital mode.
The transfer system communicates with the PLC and each of the machines via Profibus communication.
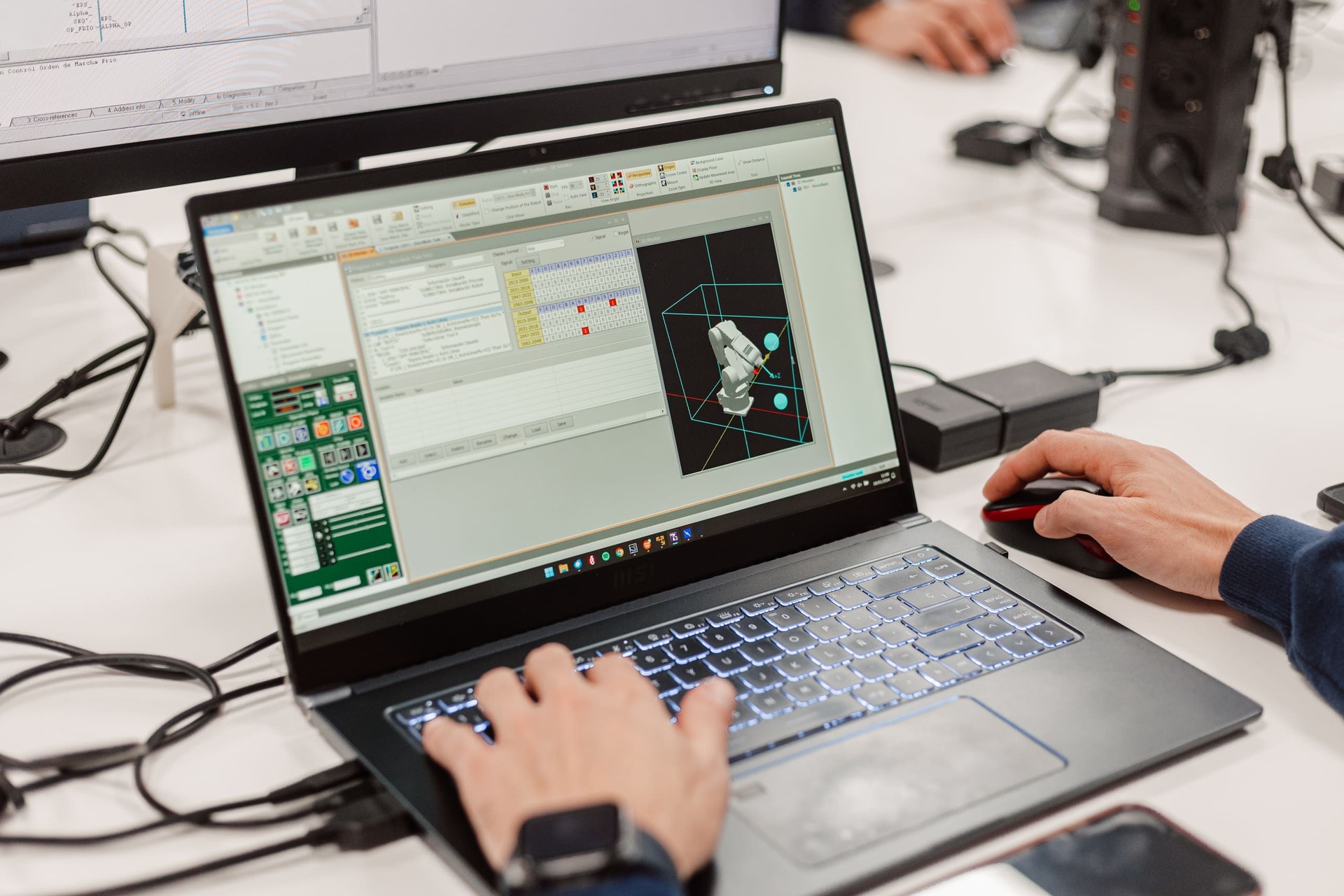
PLC and HMI Terminal
In this case, a distributed I/O unit from the original PLC that controls the entire cell has been selected. It consists of a power supply, 36 digital inputs, and 32 digital outputs. Communication between the PLC and the distributed I/O module is carried out via Profibus.
The PLC is responsible for managing commands and communication between the robot, the transfer system, the machine vision conveyor, the auxiliary feed and discharge conveyors for raw materials, and the machines that make up the production cell.
The PLC communicates with the robot via digital signals, and with the transfer system and processing machines via Profibus.
The 10” HMI terminal features a touchscreen panel. It is used to enable complete human-machine interaction, keeping the operator continuously informed about the system status. It communicates with the PLC via the MPI bus.
● Nuestros Proyectos
Últimos Proyectos
Descubre los proyectos más recientes que hemos llevado a cabo con pasión y dedicación.